09. 다시 가게 된 중국
우리에게 시간은 금과 같았기에 공장 방문 전에 마지막 작업 지시를 내리고 중국행 비행기에 몸을 실었다. 각 패턴별로 원하는 색상과 경도가 표시된 이미지를 전달하고 내가 공장에 방문한 날 바로 확인이 가능하게 해달라는 요청과 함께.
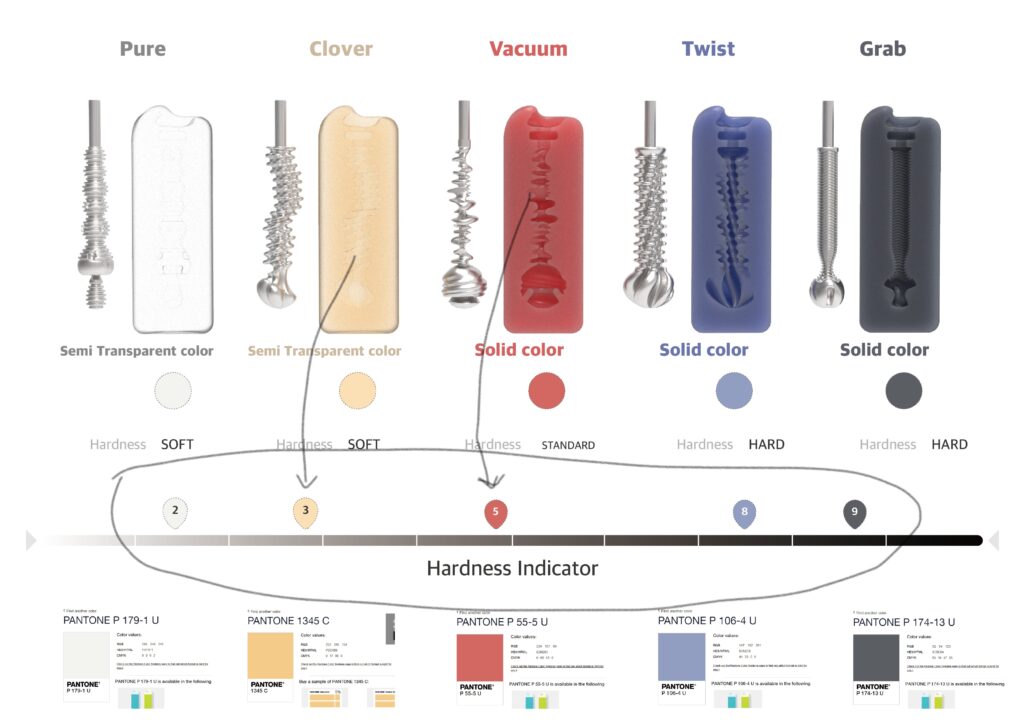
결전의 5월 28일이 밝았고 “중국행 비행기 – 중국 내륙 기차 – 공장” 에 도착하기까지 이동 시간만 7시간 이상이 소요되었지만 완벽한 제품을 조율해낼 수 있다는 기대감에 몸은 이상하게도 전혀 피곤하지 않았다. 공장에 도착했을 때는 이미 현지 담당자의 퇴근 시간이 훌쩍 지났을 때였지만 그는 반갑게 맞아주며 식사를 제안했고 앞으로의 업무 방향에 대해 의논을 하며 그들이 소위 말하는 “꽌시”를 다져갔다.
1일째
중국 공장 방문에서의 큰 뼈대는 1일 1패턴 <퀄리티 및 색상 조율>이었다. 현지에서의 조율 가능 시간은 대략 5일 남짓이었기에 하루에 1 패턴씩만 확실히 잡는다면 바로 대량생산을 진행할 수 있을 거라는 판단에서였다.
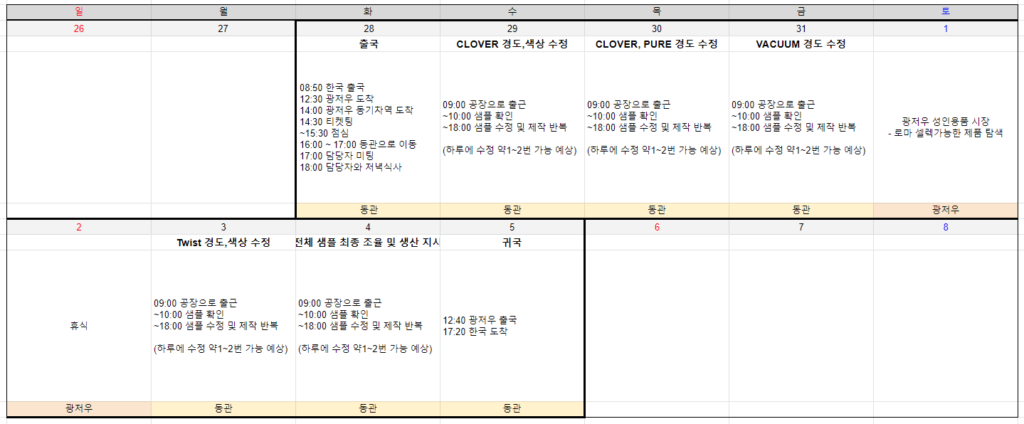
오전 일찍부터 담당자와 진행한 업무는 방문 전에 제작을 부탁했던 샘플들의 경도와 색상 체크, 그리고 앞으로 대량 생산을 진행할 때 현지에서 체크해야 하는 기준이 담긴 QC 시트 전달이었다. 8가지의 항목을 바탕으로 각 5점 만점으로 채점하되, 한가지라도 3점 이하의 점수가 나온다면 그 상품은 불량품이라는 의견을 전달하였고, 업체에서도 큰 무리 없이 요구를 수용해주었다. 4점 이상의 퀄리티에 대한 커뮤니케이션에 있어서 담당자를 설득하는데 꽤 오랜 시간이 걸렸지만 담당자 역시 우리의 퀄리티에 대한 집착을 이해해주며 논의는 긍정적인 방향으로 마무리할 수 있었다.
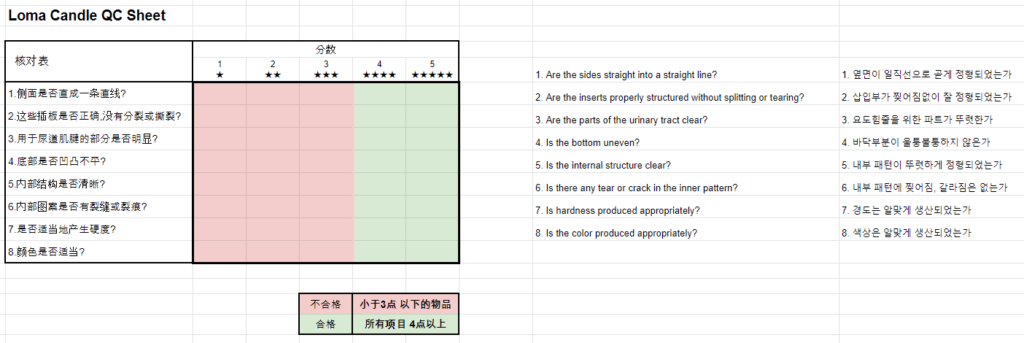
다음으로 진행한 작업은 5가지 패턴에 대한 경도 재조율 작업이었는데,(아쉽게도 체크한 샘플은 경도와 색상이 100% 마음에 들지 않았다.) 이는 우리가 직접 현지 공장을 방문하게 된 계기가 된 가장 큰 이슈 중에 하나였다. 오전 일찍 원하는 경도에 대한 샘플 제작을 요청하고 퀄리티 체크에 대한 커뮤니케이션이 끝날 때쯤 샘플을 받아 볼 수 있었는데, 처음 요청했던 바와 달리 5가지 패턴의 경도가 뚜렷하게 차이가 나지 않는 상황이었다. 경도라는 것이 단순히 생각한다면 “기본 재료에 경도를 결정하는 첨가물을 조금씩 조절하면 되잖아” 라고 쉽게 생각할 수도 있겠지만 막상 현장에서 엔지니어와 작업 프로세스를 진행해 본 결과 간단한 일이 아니었다. 이미 가장 무른 것과 가장 단단한 것 사이에 추가 첨가물의 차이가 거의 없다고 봐도 무방했고, 그 사이에서 미세하게 조정을 진행한다고 해도 실제 생산물의 경도는 거의 비슷하게 나오는 결과가 반복되었다. 5가지 경도 샘플을 제작하고 체크하길 6시간째, 도무지 진전이 보이질 않았다.
그때 사무실 문이 열리며 앞으로의 우리 제품의 퀄리티를 잡아줄 구원자가 나타나게 되는데, 그는 바로 현지 공장 생산 총 책임자였다. 선한 인상을 가진 체격이 좋은 그는 이제 근로자들이 퇴근할 시간이니 함께 저녁이나 먹으러 가자고 제안하였는데, 자신감 넘치는 그의 모습에 말없이 고개를 끄덕이며 그의 뒤를 따라나섰다. 식당에 앉자마자 자기소개와 함께 맥주 한 잔을 쭉 들이켠 그는 자신이 공장에서 총생산 책임을 맡고 있으며 이제까지는 근로자들에게 제작을 맡겼다면 내일부터는 자신이 직접 진행하겠다는 의견을 전달했다. 총 책임자 말이 그렇다는데 더 뭘 어쩌겠는가. 好(hao) “좋다”와 谢谢(xie xie) “고맙다”만 열심히 외칠 수밖에.
2일째
전날 경도 샘플에 대한 마무리를 짓지 못한 채 공장으로 향하는 발걸음은 무거웠다. 자칫 잘못하면 전체 일정이 틀어질 수 있는 상황이었기에 무슨 수를 써서라도 오늘만큼은 꼭 최종 경도 샘플을 뽑아내야만 했다. 공장에 도착한 후 눈 앞에 펼쳐진 상황에 깜짝 놀랄 수밖에 없었는데 전날 호탕하게 웃으며 연거푸 맥주를 마신 뒤 비틀거리며 돌아간 생산 책임자가 이른 아침부터 공장에서 땀을 흘리며 샘플 제작에 몰두하고 있었던 것이었다. 나를 발견한 그는 역시나 호탕한 웃음을 보이며 자기가 거의 샘플 생산을 끝냈다며 조금만 기다리라고 말하곤 다시 제작에 집중했다.
전날 만족할만한 경도별 샘플을 뽑아내진 못했지만 그 자리에 멈춰 있을 수만은 없었다. 다행히도 중국 공장은 한국 공장과 다르게도 각각 파트별(색상, 경도, 생산, 퀄리티 등) 담당자가 따로 있었고 우린 경도를 뒤로한 채, 바로 Twist의 색상 조율 작업에 들어가기로 했다.
팬톤 컬러 칩을 통한 컬러 칩 전달, 컬러 칩을 통한 큰 가이드라인을 제시하고 그에 맞춰 원하는 색상을 미세 조율. 이는 제품을 생산하기 전에 금형을 만들고 금형에서 원하는 T1 사출품의 색상을 뽑기 위한 기본적인 프레임 워크이다. 물론 이번에도 그렇게 진행을 했고.
근데 원하는 오나홀 색상을 생산하기 위해서는? 컬러 칩? 컬러 샘플? 다 필요없다. 물론 내가 원하는 색상이 이런 느낌의 색상이라는 큰 가이드라인을 제시할 수는 있겠지. 우리가 Twist에 원했던 색상은 딥하면서도 채도가 어둡지 않은 뚜렷한 파랑 계열의 색상이었는데 컬러 칩으로 말하자면 PANTONE P 106-4U 같은 색상이었다. 하지만 한국에서 몇 번의 샘플을 받는 동안에도 색상이 전혀 고쳐지지 않았고 이번에 현지를 방문한다면 Twist의 색상부터 바로 잡겠다고 마음먹었었다. 여러 번의 제품 개발 경험을 가지고 있었던 터라 당연히 자신 있게 작업장에 들어가서 담당자와 색상 조율 작업을 한 나는 정말 놀라운 경험을 했다. 미리 조색해놓은 재료의 색상이 재료가 성형되는 순간의 온도에 따라 가지각색으로 변하는 것이었는데, 파란색도 딥한 파란색, 연한 파란색, 흐린 파란색 아주 가지각색이었다.
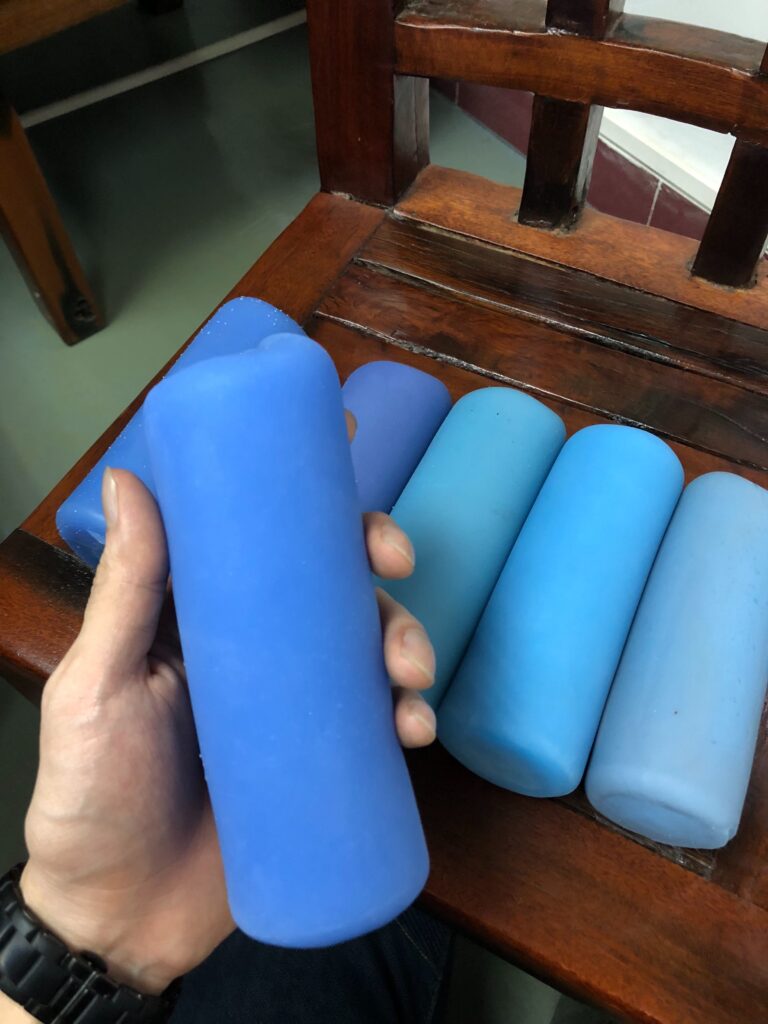
그럼 이렇게들 말할 것이다. “어? 그럼 애당초 재료가 성형되는 순간의 온도를 200º, 210º 로 고정해놓으면 풀 수 있는 쉬운 문제잖아?” 맞다. 나도 그렇게 생각했으니까.
이때까지만 해도 우리가 추구하는 가장 큰 목표점은 “높은 퀄리티” 단 한 가지였다. 높은 퀄리티를 통해 완벽한 제품을 만들 수 있다면 생산 단가보다 가장 우선시 되어야 할 가치였다. 따라서 우리는 220º로 성형 온도를 고정하고 색상을 뽑아냈다. 매우 만족스러웠다. 내가 원하던 영롱한 바로 그 색 이었으니까. 이는 나중에 부메랑이 되어 돌아오는데, 그건 뒤에서 다시 얘기하겠다.
색상에 흡족해하고 있을 때쯤 그가 들어왔다. 오전 내내 자신이 흘린 땀을 증명하는 듯한 양손의 샘플 5개와 함께. 무척이나 자신만만한 표정의 그가 제시한 샘플들은 전날 내가 받아본 샘플들과 확연히 달랐다. 퀄리티도 퀄리티 뿐일 더러 전날에 해결하지 못한 패턴별 경도가 달라져 있었다. 하지만 여전히 기대치에는 미치지 못했다. 나는 Pure와 Clover 간의 경도 차이를 원했고 약 4정도의 경도를 가져야 할 Clover가 5의 경도를 가진 Vacuum과 확연한 경도 차이가 나기를 바랬다.
그런 우리의 의견을 들은 생산 책임자 역시 처음에는 곤혹스러운 표정을 감추지 못했다. 그도 그럴 것이 그렇게 자신만만하게 들고 온 샘플이 당차게 까여버렸으니까. 하지만 그는 프로였다. 특유의 웃음과 함께 기다리라고 다시 만들어오겠다며 그는 그렇게 사라졌다.
2일째 업무를 마치며 식사를 하던 중 담당자가 기분이 다운되어있던 내게 물었다. 그가 원하는 샘플을 못 뽑아낼까 봐 걱정되냐고, 그는 벌써 12년째 생산 파트를 맡은 전문가이니 한 번 더 믿어보라고. 왠지 모르게 느껴지는 신뢰감에 우린 함께 웃었고 그렇게 2일째 밤이 지나가고 있었다.
Editor : Product Designer Grey
다음 화로 이어집니다.